EJOFORM®
Specification
-
Overview
- 100% 匹配应用场景
- 降低材料和库存成本
- 由于多功能性,有很大的成本节约潜力
- 安装简单
- 替代机加工件
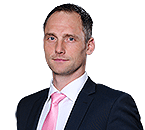
Torsten Lückel
Product Manager
EJOFORM®“产品理念”
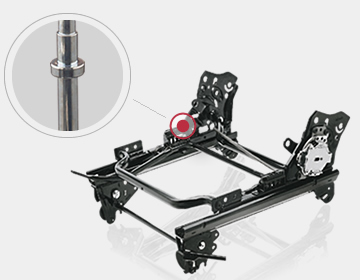
钢制或者铝制的冷镦成型件的应用场合种类几乎是无限的,EJOFORM®产品总是为客户提供创新且符合客户标准的紧固与设计方案。这些设计面向很宽的需求,例如固定器,限位螺栓,隔套,调节元件或是煞车系统上的安全相关组件。每一个零件都使用多工位冷镦成型技术制造。 采用这种技术,圆形截面的线材能够在几个冷镦步骤之后被冷成型为复杂的零件。
EJOT应用工程师将帮助您实现最大潜力的成本节约与应用优化。从产品概念开发到实施量产,为客户提供贯穿整个产品周期的服务是毅结特的重要职责
“可以计算的”的优势
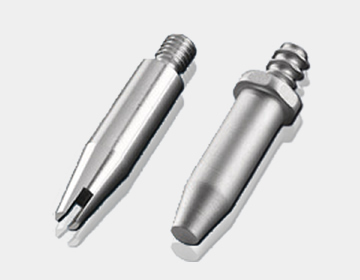
EJOFORM®特殊优化的可能性最好是通过一个例子来说明。使用5道工序的冷镦技术的EJOFORM®冷成型件(右侧图),相较于车加工件(左侧图)节约了大约25%的材料。同时也产生了其他的优势。例如,毅结特的外六角驱动和机加工件的一字驱动相比可以传递更大的扭矩。EJOFORM®同时也可以配备不同的螺纹类型(这里是DELTA PT®),以满足所有可能的需求和材料。
使用EJOFORM®产品带来的经济优势来源于其生产工艺。相对较高的初期摸具成本也被分摊到后续生产的零件中, EJOFORM®高效和经济的生产过程使得其拥有成本优势。和车加工或者铣价格相比,冷成型设备产出更多,这为客户带来了明显的成本结构改善。当零件产量很大时,这一点变得尤为明显。甚至在某些设计下可以实现节约80%的材料成本
多种多样的“成品”
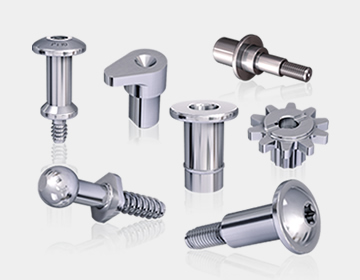
精密制造的EJOFORM® 冷成型零件可以通过各种工艺进行补充、细化和改进。根据具体的应用和独立的要求,毅结特提供单一来源的经优化的技术。
为了实现例如钻孔,间隙槽或不寻常的轮廓,具有复杂几何形状的零件可以进行部分机加工。内螺纹采用切削或者挤压成型,也可根据客户要求来实现。在毅结特,EJOFORM®FORGINGS冷成型件是实现这些附加技术可能性的总和。
EJOFORM® 可以使用多种材料制造。主要使用普通钢和铝合金材料。但是如果需要,零件也可以由不锈钢制成。通常的调质强度等级满足DIN ISO 898 标准,对于特殊螺纹,采用毅结特公司标准。镀锌层根据DIN EN ISO 4042制造,其他的表面处理,例如需要达到1000小时耐盐雾性能的,也是可以选用的。